A university
professor uses Saber Designer to help Ford Motor Company and his
students gain new perspectives on the engineering design process. At
Ford, his simulations identified the previously overlooked wire harness
as having a significant impact on overall system performance. Using
Saber, Dr. Ash discovered that the wiring harness significantly impacted
overall system performance, a fact that went undetected by traditional
subsystem simulations.
I believe
that this is the first automotive design effort that models the total
vehicle system by using mostly generic device models from the Analogy
library.
Dr. Armand
Ash-Rafzadeh
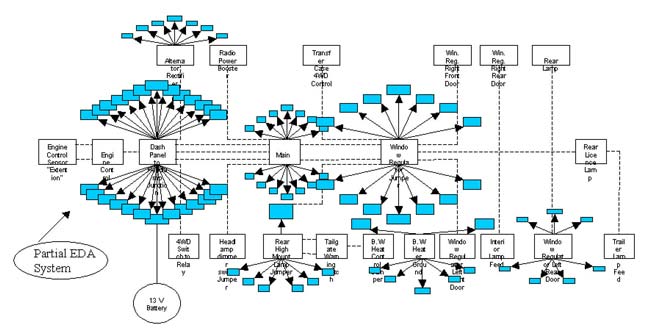
Total Vehicle Electric Design
Automation (EDA)
System Engineering Approach
Most of us take our cars for granted. We
open the door, adjust the seat and turn the key in the ignition. The
engine fires up and we pull out into the street. All the vehicle
electronics - the power door locks, the seat positioner, the ignition
controls, the anti-lock braking system, even the headlights and radio —
work as expected. But designing all these individual subsystems to work
in perfect harmony is a tremendously complicated challenge for
automotive engineering teams.
Faced with the rapidly increasing
complexity of its electrical subsystems, Ford Motor Company called on
noted professor and consultant Dr. Armand Ash-Rafzadeh (“Dr. Ash”) to
develop an improved design process. The goal was to expand Ford’s design
awareness so they could manage the performance of systems as a whole —
not just the individual performance of subsystems. Ford’s prevailing
design program focused on subsystems, rather than total system and
connectivity between subsystems. “The old methods didn’t take the wire
harness into account. Design and testing were fragmented,” said Ash. The
individual systems were separately designed, simulated, prototyped, and
modified. This caused problems with simulation because there was no way
to account for the interconnections between the vehicle subsystems. Ash
faced this challenge by developing a new design process he called the
“Wire Harness Centric View” (WHCV). This new methodology isolates each
wire harness rather than each subsystem. Thus, the design perspective
becomes essentially that of a wire harness connected to all of its
components. To simulate the complex interactions of these linked
systems, Dr. Ash turned to Analogy’s Saber Designer.
“We put the system together and were very
successful,” said Ash. “I believe that this is the first automotive
design effort that models the total vehicle system by using mostly
generic device models from the Analogy library.” Using WHCV helped
identify the crucial circuit modifications needed, and it did so very
early in the design cycle.
Ash’s consulting firm, Mechatronics, Inc.,
placed eight Saber-trained employees as subcontractors to Ford. Using
the lessons learned from the WHCV program, Ash began specifying the
device models needed for a Total Vehicle Analysis. The first step was to
apply Ash’s newly- created Vehicle Element Identification Process (VEIP).
VEIP was used to develop a list of “commodities” – components in the
vehicle that were to be simulated — and a complete specification of the
simulation model. In addition to generating the requirements for
Analogy’s MAST® modeling, VEIP also simplified data management and the
creation of schematic symbols.
Ash began by using Saber and his new
process to analyze a complete steering system. The process used vehicle
sensor data, the digital signal processing capabilities of MATLAB®, and
the system and mechatronic simulation capabilities of Saber and MAST.
The objective was to identify the source of noise that occurred at low
speeds and disrupted the steering-fluid flow rate. Results from the
Saber simulation allowed designers to modify the control circuit to
maintain the proper fluid levels. On subsequent projects, Ash and his
team made full use of Saber’s capabilities. “We used everything [in
Saber] that there was,” said Ash. “Monte Carlo was most helpful. We
evaluated the negative performance impacts that came from the
interaction of component tolerances. We also quantified the contribution
of each component or component cluster.” Ash also used Monte Carlo
analysis to study how component combinations can affect subsystem
performance. “We can measure performance levels and buy the appropriate
quality of components needed by that particular subsystem.” “My ultimate
goal is to get as many companies involved in the VEIP process as
possible,” said Ash. “We’d like to provide this solution to other
companies in the industry. Ford is fanatical about this. They realize
that this is a very important strategic tool for automotive design. It
doesn’t only perform systems analysis; it changes the whole design
culture. It gets you involved in data management, data structures, and
many other processes. The automotive industry knows the importance of
this, but few companies have made the necessary commitment to change. It
hasn’t yet been integrated into their engineering cultures.” Based on
his successes at Ford, Ash obtained Saber as a teaching tool for his
classes at the University of Detroit. He identified promising graduate
students and brought them into his projects.
S A B E R S U C C E S S E S
“Using Saber helps my students become
really ingenious. It brings out the ‘real’ engineer in them and lets
them apply their skills with greater creativity and effectiveness. Those
who become proficient with Saber really gain a higher-level
understanding of the systems they work with.” |